LEAN PRODUCTION
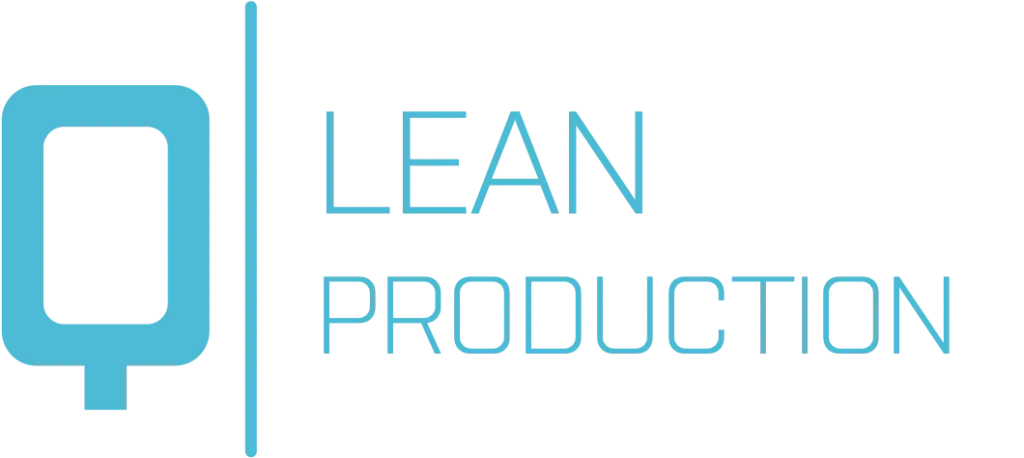
The value chain of modern manufacturing is similar to the value chain of software development and with the increasing use of software in production systems, these value chains are moving closer together. Since we know both sides of the process, we know where optimization can be made and waste can be reduced.
- Reduction of downtime
- Optimization of OEE (Overall Equipment Efficiency)
- Increase of production performance
The 5 Lean Principles
Define Value
Definition of customer value and breakdown your costs and services.
Value Stream
Identify and inspect your value stream and eliminate waste in your production system.
Production Flow
Establishing of a continuous production process.
Pull Principle
Only produce what has been ordered by your customer. Pull orders don't push them.
Pursue Perfection
Establish a continuous improvement on the way to perfection.
Our Guiding Principles
Our guiding principles for lean production are aligned with the VDI 2870 norm (LPS) and consider all aspects of a modern production system.
Avoid waste
Eliminate all non-value-adding tasks and processes within your production process and define necessary activities that ad customer value.
Use available resources
With more effective processes the use of resources can be optimised, additionally we combine these aspects with green management to reach a sustainable production process.
Standardize
With the help of standardising we can help you optimise similar and repeating processes and tasks. This eliminates non-value-adding tasks and increases stability.
Improve continuously
Reach perfection and never give up - with this in mind we establish a framework together with you to continuously improve your production.
Follow the zero defect principle
Remove defects and impediments where they arise. Additionally find ways to reduce mistakes within the process chain.
Use the pull principle
Don't push the order - the production pulls it through when it has been ordered by a customer. This reduces warehousing costs and eliminates time for process control. Do it when need it.
Follow the flow
With reduction of interim storage and increased information flow we reduce your lead time by realising a fast, continuous and low-turbulence material flow.
Lead motivationally
We see employees of a company as crucial resources for innovative concepts and continuous process improvements. For successful implementation, it is necessary to establish and live this attitude.
Your benefits
Detection and elimination of waste in time and process is key focus of our Lean Production Consulting. Together we find the parts in your production process that your customer is not willing to pay for and optimize your production process towards a sustainable future.
After consolidation of all processes, parameters and tasks along the value chain of your production, we are able to identify and concentrate on the removing of those wasting items like:
- No overproduction
- Reduction of „on-hold“ products
- Improved transport without intermediate storage
- Reduction of waiting time
- Reduction of complexity
- No long ways
- Less mistakes
- Improved use of potential